Metal Stamping: Advanced Techniques for Getting Accuracy and Performance
Advanced Techniques in Steel Stamping for Precision Production
In the realm of accuracy production, the advancement of metal stamping methods has been a pivotal force in achieving exceptional degrees of accuracy and performance. As industries constantly demand better tolerances and detailed designs in their steel components, the mission for advanced techniques in metal marking has intensified. From the use of sophisticated multi-stage marking procedures to the integration of sophisticated automation innovations, the landscape of steel marking is undertaking a profound change. In this dynamic field, the merging of advancement and accuracy is improving the opportunities of what can be attained in steel fabrication.
Advanced Multi-Stage Stamping Procedures
Reviewing the ins and outs of advanced multi-stage stamping procedures discloses the innovative techniques employed in modern manufacturing methods. Metal Stamping. Multi-stage marking is a complicated process that entails numerous actions to change a level sheet of steel right into a last stamped item. Making use of dynamic passes away, where various procedures are executed at each phase of the marking process, permits for high accuracy and effectiveness in the production of intricate steel parts
During the first phases of multi-stage marking, the level steel sheet is fed into the stamping press, where a series of passes away are used to cut and shape the product. Succeeding phases include extra forming, bending, and punching procedures to more improve the part. Each stage is carefully designed to build upon the previous one, bring about the production of intricate geometries with tight tolerances.
Advanced multi-stage marking procedures require a high level of knowledge and precision to make certain the top quality and consistency of the stamped parts. By making use of advanced machinery and tooling, suppliers can generate a variety of steel elements with efficiency and precision.
Precision Tooling Innovations
Accuracy tooling advancements have revolutionized the steel stamping sector, improving efficiency and top quality in manufacturing processes. These innovations have substantially affected the means metal components are created, resulting in greater precision and uniformity in the final items. One essential innovation is the advancement of computer numerical control (CNC) innovation in tooling layout and fabrication. CNC systems enable detailed designs to be converted directly into tooling, guaranteeing precision and repeatability in the marking process.
In addition, the integration of sensors and real-time monitoring capabilities in precision tooling has allowed producers to find and resolve concerns without delay, minimizing downtime and reducing scrap rates. By incorporating smart modern technology right into tooling, drivers can maximize criteria such as stress, rate, and positioning during the stamping operation, causing boosted item top quality and boosted efficiency.

Automation in Metal Stamping
The evolution of accuracy tooling technologies in the steel marking market has led the way for substantial innovations in automation, changing the manufacturing landscape towards increased efficiency and productivity. Metal Stamping. Automation in metal stamping entails making use of advanced machinery and robotics to perform numerous jobs typically executed by human drivers. This shift towards automation supplies many benefits, consisting of enhanced precision, much faster manufacturing cycles, and decreased labor prices
One secret aspect of automation in steel stamping is the execution of computer system numerical control (CNC) systems, which make it possible for accurate control over the marking process. CNC technology permits the creation of facility and elaborate steel get rid of regular high quality. Additionally, automated systems can be configured to run continuously, causing higher result rates and shorter lead times.
Furthermore, automation boosts work environment safety by minimizing manual handling of hefty products and reducing the threat of accidents (Metal Stamping). As producing sectors remain to accept automation, the future of steel stamping holds excellent promise for even better efficiency and advancement
High-Speed Stamping Strategies
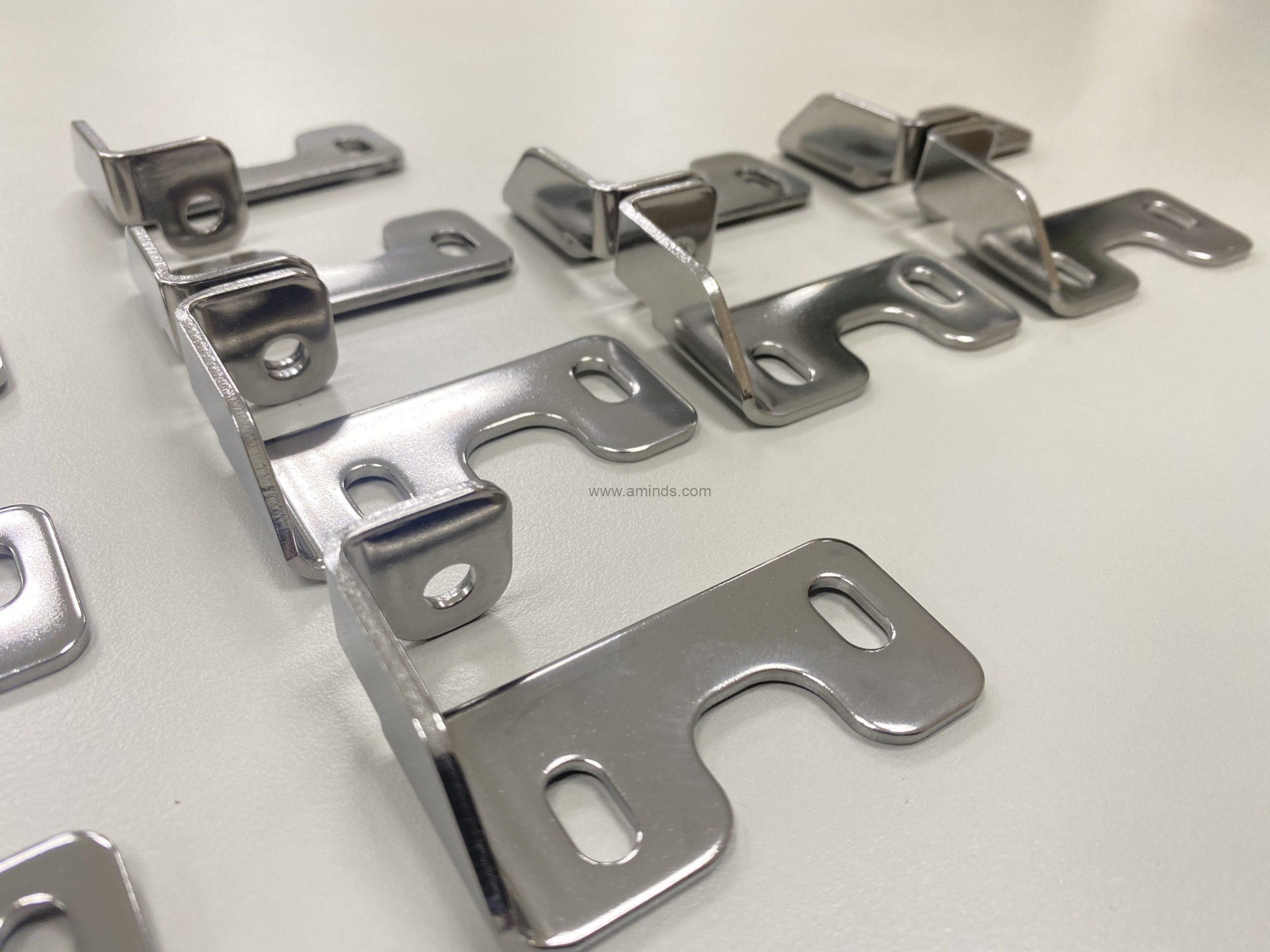
One of the primary advantages of high-speed stamping methods is the capacity to generate a big quantity of parts in a much shorter amount of time contrasted to standard marking methods. This increased productivity not only allows manufacturers to meet tight manufacturing target dates yet additionally makes it possible for cost financial savings via economic situations of range. Furthermore, high-speed stamping can help in reducing material waste by maximizing the product use during the stamping procedure.
In addition, high-speed marking methods go to my site typically integrate innovative features such as fast die modification systems and real-time tracking capabilities, better boosting the general efficiency and adaptability of the steel stamping procedure. As modern technology remains to advance, high-speed marking is expected to play an essential role in driving the future of accuracy manufacturing.
Quality Control in Stamping Procedures
Effective quality control procedures are vital for guaranteeing the reliability and uniformity of metal marking operations. Quality assurance in marking operations entails a series of systematic procedures aimed at spotting and preventing issues in the made components. One crucial element of quality assurance in steel marking is using innovative inspection why not check here strategies such as optical inspection systems and coordinate measuring equipments (CMMs) to confirm the dimensions and tolerances of stamped parts.
Furthermore, quality control steps in marking procedures typically consist of the execution of analytical procedure control (copyright) approaches to keep an eye on the production process in real-time and guarantee that it continues to be within appropriate limits. By examining data and recognizing trends, suppliers can proactively resolve any type of discrepancies from the preferred quality criteria.
Furthermore, quality assurance in metal marking procedures likewise entails extensive product screening to make certain that the raw materials made use of satisfy the needed requirements for the marking process. This might include carrying out product hardness examinations, tensile strength examinations, and dimensional examinations to assure the top quality and stability of the stamped elements. Overall, implementing durable quality assurance official source steps is critical for attaining premium stamped parts continually.
Verdict
Finally, advanced techniques in metal marking play a critical duty in accuracy production procedures. Via multi-stage marking processes, cutting-edge tooling remedies, automation, high-speed methods, and extensive quality control steps, producers can achieve higher levels of precision and effectiveness in their operations. These developments in metal marking innovation have made it possible for companies to create complex get rid of tight resistances, inevitably resulting in enhanced product high quality and customer complete satisfaction in the manufacturing market.